Metal Separators for Bulk Material Handling
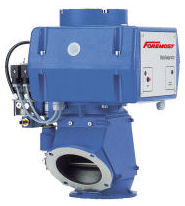
In a typical plastic recycling system, the raw material will flow from the the top of the helical lifting conveyor into a metal separator. In some applications, using gravimetric dosing, a second metal separator is introduced that will move the rejected material from the first separator kernel by kernel to the second separator. Without a second separator the separation of metal is not as accurate or precise, and the material lost can be as high as 5,000 l / week. With a second separator, material loss is reduced to a little as 40 l/week. In just a few months, this two tiered solution will pay for itself.
Within the compact series of metal separators, we are also pleased to announce the new VA Series metal separation solution that is even more compact, sturdy and reliable. Available in diameters of 35, 50, 70 and 100 mm, these robust units can handle material throughput levels ranging from 1,000-8,000 l/h. Depending on the model used, these separators offer sensitivity levels that can an detect metals ranging in size from 0.5 to 1.3 mm.
In a typical plastic recycling system, the raw material will flow from above through the metal separator into the funnel. The white rubber collar isolates any vibrations and oscillation.
The compact series of metal separators is available in 100 to 350 mm. It features an extremely sturdy steel setup rack, and an extremely low knock sensitivity in a fully encapsulated high quality pick up coil. These large scale models are easy to operate and put into commission. With a calibration free sensor coil, these separators offer sensitivity levels that can an detect metals ranging in size from 0.5 to 2.5 mm. Available in diameters of 35, 50, 70 and 200 mm, these robust units can handle material throughput levels ranging from 20000 to 290000 l/h.